Twoje Centrum Fitoterapii i Ziołolecznictwa
Interesujesz się naturalnymi metodami leczenia? Odkryj fitoterapię i ziołolecznictwo na aimis-fyt.eu.
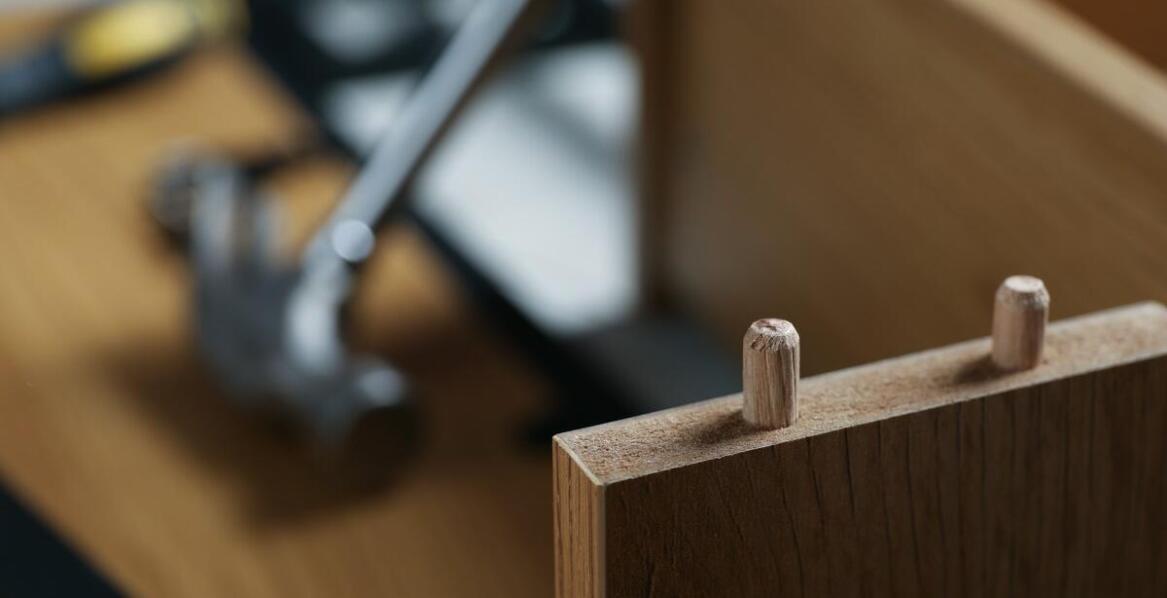
W jaki sposób lanca pianowa może zwiększyć efektywność pracy serwisów sprzątających?
Lanca pianowa to innowacyjne narzędzie, które znacząco zwiększa efektywność pracy serwisów sprzątających. Dzięki swojej konstrukcji umożliwia równomierne rozprowadzenie detergentu, co przyspiesza proces czyszczenia i poprawia jakość usługi. W artykule omówimy, jak lanca pianowa wpływa na wydajność o
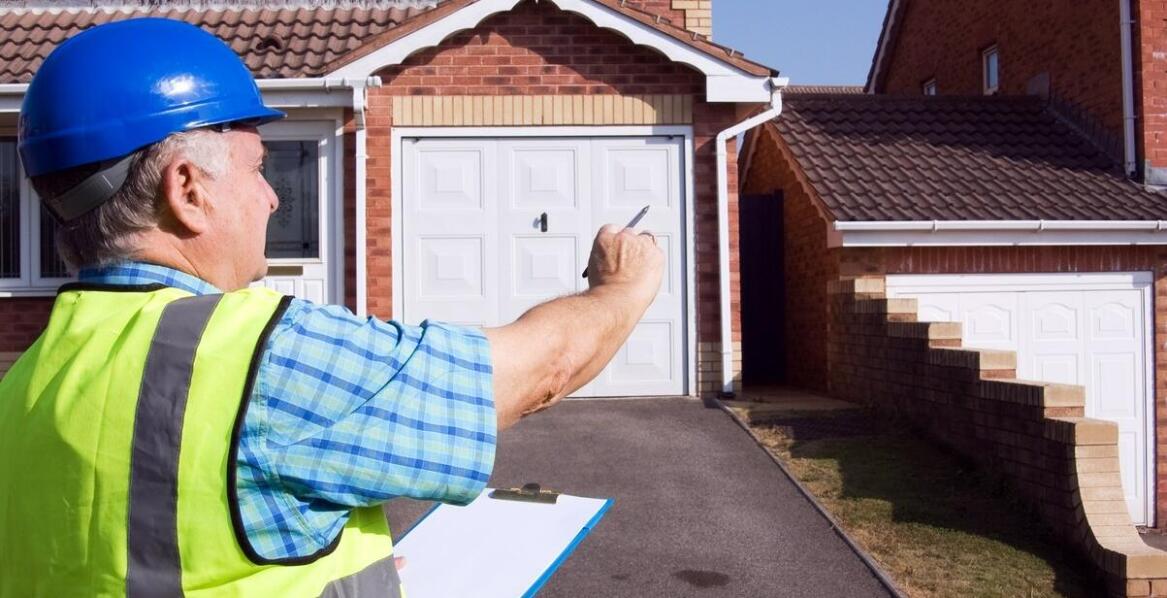
Bezpłatny pomiar i prezentacja stolarki otworowej: jak to wygląda w praktyce?
Decydując się na zakup bram garażowych Wiśniowski w Warszawie, warto skorzystać z możliwości bezpłatnego pomiaru i prezentacji stolarki otworowej. Dzięki temu klient może dokładnie zapoznać się z ofertą, a także uzyskać fachowe porady dotyczące wyboru odpowiedniego produktu. Warto dowiedzieć się, ja
Artykuły ostatnio dodane
Produkty i usługi dla każdego
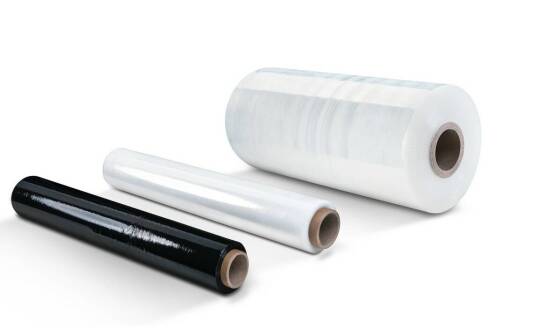
Folia stretch czarna 3 kg jako ochrona przed kurzem i wilgocią
Folia stretch czarna 3 kg to wszechstronny materiał, który znajduje zastosowanie w wielu branżach. W artykule omówimy jej właściwości, które sprawiają, że stanowi idealne rozwiązanie do ochrony przed kurzem i wilgocią. Dzięki elastyczności oraz wytrzymałości skutecznie zabezpiecza różnorodne przedmi
Usługi i produkty remontowo-budowlane
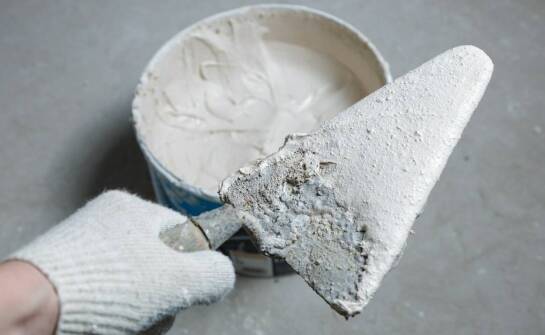
Jakie korzyści płyną z użycia kleju białego w renowacji budynków?
Klej biały to uniwersalny materiał, który sprawdza się w różnych aspektach renowacji budynków. Jego właściwości czynią go doskonałym wyborem do prac budowlanych i remontowych. W porównaniu do innych rodzajów klejów wyróżnia się łatwością aplikacji, szybkim czasem schnięcia oraz odpornością na wilgoć
Odzież, obuwie i dodatki
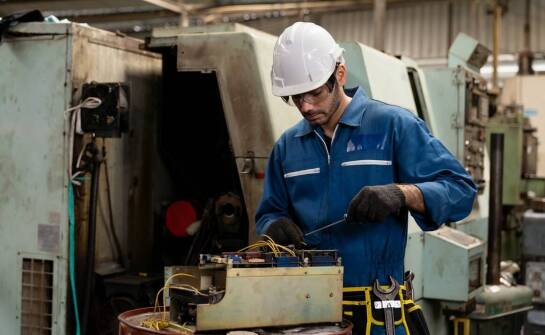
Odzież robocza antyelektrostatyczna – jak wpływa na bezpieczeństwo pracowników?
Odzież robocza antyelektrostatyczna jest niezbędna dla ochrony pracowników przed wyładowaniami elektrostatycznymi, które mogą prowadzić do poważnych konsekwencji zdrowotnych. Właściwy dobór tego rodzaju odzieży minimalizuje ryzyko wystąpienia tych zjawisk, co przekłada się na bezpieczeństwo w miejsc
Nieruchomości, zarządzanie budynkami i obiektami
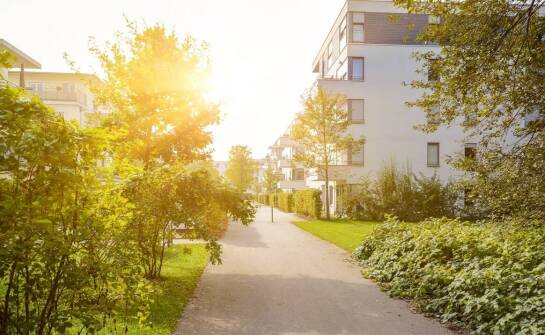
Jakie są korzyści z przepisania umów na dostawę mediów po zakupie nieruchomości?
Przepisanie umów na dostawę mediów po zakupie nieruchomości to kluczowy krok, który zapewnia ciągłość usług oraz komfort nowych właścicieli. Właściwe zarządzanie tym procesem pozwala uniknąć problemów z dostawcami oraz gwarantuje dostęp do niezbędnych usług, takich jak energia elektryczna, woda czy
Ochrona zdrowia i uroda
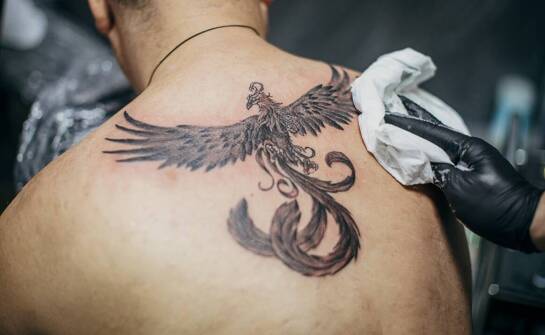
Jak wygląda proces gojenia tatuażu i jak długo trwa?
Proces gojenia tatuażu to kluczowy etap, który wpływa na ostateczny wygląd i trwałość dzieła na skórze. W trakcie tego czasu organizm reaguje na wprowadzone tusze, a skóra przechodzi przez różne fazy regeneracji. Gojenie rozpoczyna się od momentu wykonania tatuażu i obejmuje etapy takie jak strupkow
Transport, logistyka i pojazdy
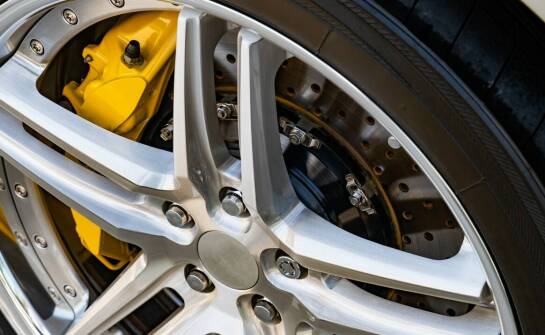
Dekielki BMW – jak wpływają na pierwsze wrażenie o samochodzie?
Dekielki BMW to istotny element wpływający na pierwsze wrażenie o pojeździe. Podkreślają jego charakter, a także mają znaczenie dla właścicieli. W artykule omówimy różnorodność dostępnych modeli oraz ich wpływ na postrzeganie marki. Zwrócimy uwagę na to, jak te akcesoria mogą wpłynąć na estetykę sam
Gastronomia, artykuły spożywcze
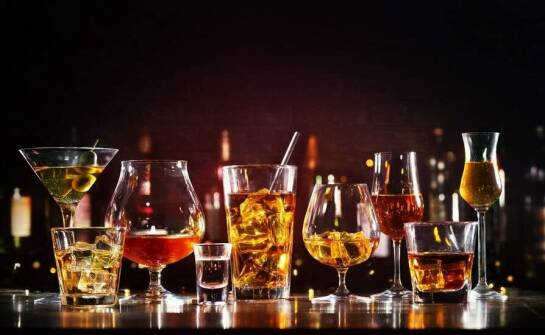
Najlepsze drinki z Bacardi
Bacardi to jedna z najbardziej znanych marek alkoholi na świecie, której głównym produktem jest karaibski rum. Wyrób ten kojarzy się z egzotycznymi wakacjami, słońcem i plażą, a przede wszystkim z pysznymi drinkami. W tym artykule przedstawiamy siedem najlepszych drinków z Bacardi, które warto sprób
Turystyka, noclegi i wypoczynek
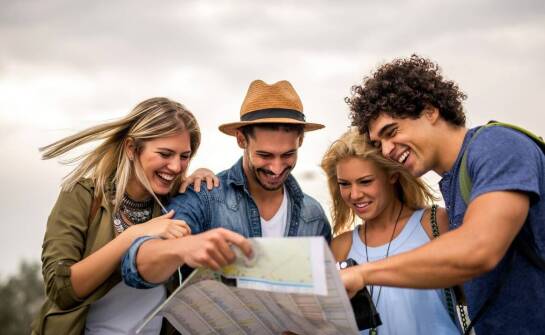
Dlaczego warto skorzystać z usług przewodników na trasie z lotniska Fiumicino do Rzymu?
Podróż z lotniska Fiumicino do Rzymu może być wyzwaniem, zwłaszcza dla nowicjuszy. Wsparcie przewodników znacząco ułatwia ten proces, eliminując stres związany z transportem. Eksperci nie tylko zapewniają sprawne przemieszczanie się, ale również wprowadzają w lokalną kulturę i historię. Dzięki temu
Zakupy, kultura i rozrywka
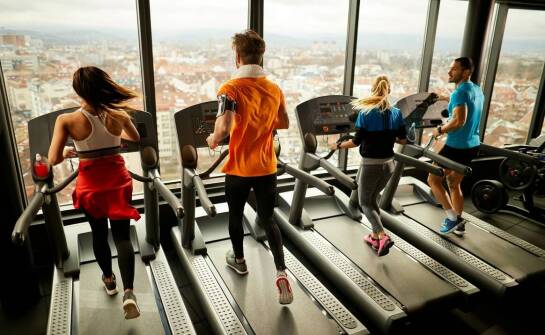
Jakie zmiany w grafiku zajęć można oczekiwać w siłowni mogilskiej podczas sezonu letniego?
W okresie letnim siłownie wprowadzają zmiany w harmonogramie zajęć, aby lepiej odpowiadać na potrzeby klientów. W siłowni mogilskiej można spodziewać się nowych grupowych treningów oraz modyfikacji godzin otwarcia. Te zmiany mają na celu uczynienie oferty bardziej dostępną i atrakcyjną dla osób korz
Elektronika, AGD, narzędzia
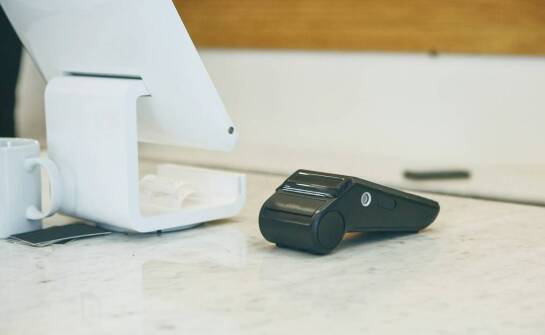
Kasy fiskalne dla e-sklepów – co warto wiedzieć przed zakupem?
Kasy fiskalne odgrywają kluczową rolę w e-sklepach, umożliwiając prawidłowe funkcjonowanie oraz spełnienie wymogów prawnych. Są niezbędne do rejestrowania sprzedaży i wystawiania paragonów, co jest wymagane przez przepisy prawa. Dzięki nim przedsiębiorcy mogą prowadzić rzetelną księgowość oraz kontr
Media i badanie rynku
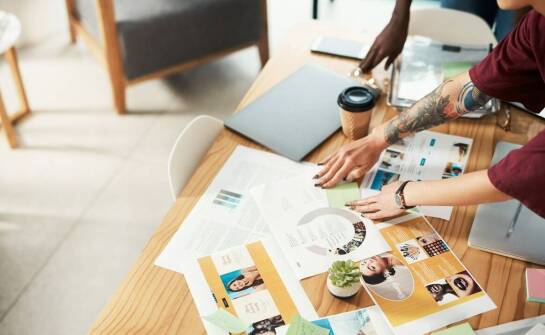
Jak wykorzystać kubki reklamowe w działaniach e-commerce?
Kubki reklamowe to nie tylko praktyczne przedmioty, ale również efektywne narzędzia marketingowe. Ich unikalne cechy przyciągają uwagę klientów i zwiększają rozpoznawalność marki. Różnorodność kształtów oraz kolorów sprawia, że stanowią doskonałe rozwiązanie w kampaniach reklamowych. Personalizacja
Nauka i szkolnictwo
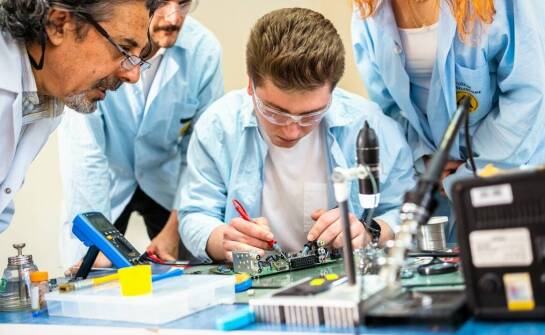
Dlaczego maszyna elektrostatyczna służy do nauki o ładunkach elektrycznych?
Maszyna elektrostatyczna służy do istotnego znaczenia w edukacji fizycznej, umożliwiając uczniom zrozumienie zasad ładunków elektrycznych. Dzięki niej mogą obserwować efekty działania ładunków, co znacznie ułatwia przyswajanie wiedzy. Praktyczne narzędzia w nauce odgrywają kluczową rolę w procesie e
Finanse i ubezpieczenia
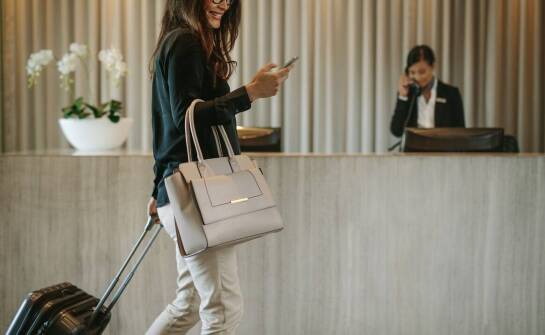
Ustalenie zasad współpracy z biurem rachunkowym - kluczowe kwestie
Współpraca z biurem rachunkowym może być kluczowa dla sukcesu firmy, zwłaszcza w przypadku małych i średnich przedsiębiorstw. Wybór odpowiedniego podmiotu jest istotny ze względu na różnorodność usług oferowanych przez takie biura. Możemy tu wymienić prowadzenie księgowości, doradztwo podatkowe, obs
Wnętrza - wyposażenie i wystrój
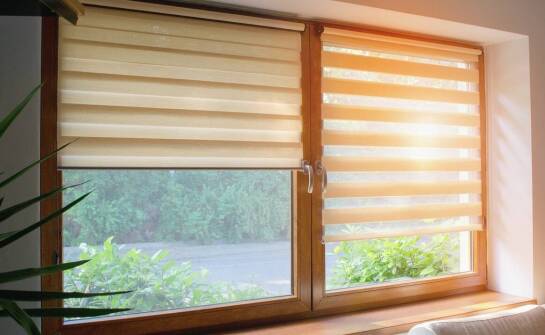
Rolety okienne wewnętrzne jako sposób na kontrolowanie światła i prywatności
Rolety okienne wewnętrzne pełnią istotną rolę w aranżacji wnętrz, łącząc funkcjonalność z estetyką. Dzięki nim można kontrolować ilość światła wpadającego do pomieszczeń oraz zapewnić mieszkańcom prywatność. Wybór odpowiednich modeli wpływa na atmosferę i komfort użytkowania przestrzeni. Zrozumienie